Ford Trains Human 'Gremlins' To Find Faults
- Aaron Alleyne-Wake
- Nov 17, 2016
- 1 min read

As you can imagine quality control is a big thing for car manufacturers, just one faulty part can play havoc so it's important it's done right first time. This is why Ford has trained members of its Valencia plant to place faulty parts on the assembly line to ensure that they are snubbed out before the car leaves the plant.
The rogue parts include incomplete steering wheels, faulty engine components and even incorrect dashboards are put in place to make sure they are recognised. Call my picky, but I'm sure it wouldn't take long to notice a steering wheel isn't complete? To help find the faults, Ford uses Vision System photographs (an industry-first) to check and track every single part of the car as it passes through the production line.
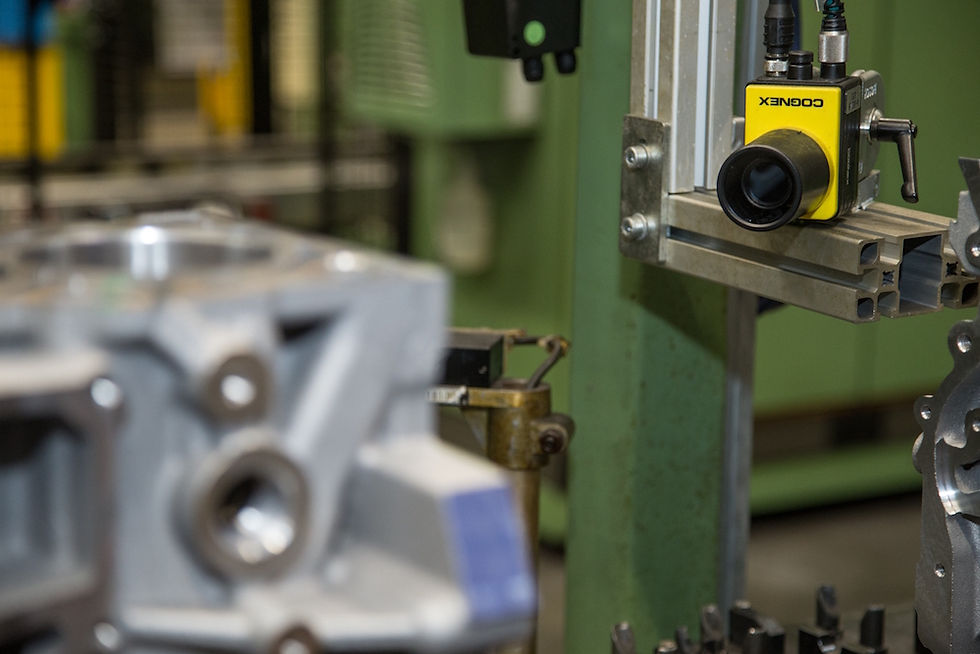
“The Vision System is crucial to ensuring every single part of each vehicle is just right,” said Garciandia, technical specialist, Valencia Engine Vision System, Ford of Europe. “The ‘Gremlin Test’ means we can ensure the system is working perfectly. It is a game with a very serious point; we are making them harder to spot all the time.”
The way in which we all use digital cameras has totally changed the way we record our daily way of life, and is now transforming the way we build engines and cars,” said Garciandia. “But we also have to test the tests, and we are doing this in a way that is very simple, but which we believe is unique in the auto industry.”

Comments